KraussMaffei impulsa construcción ligera en aeronaves eVTOL con FiberForm
KraussMaffei y el NIAR desarrollan una nueva tecnología, FiberForm, que reduce a dos minutos la fabricación de componentes estructurales aeronáuticos, mejorando la eficiencia y sostenibilidad.
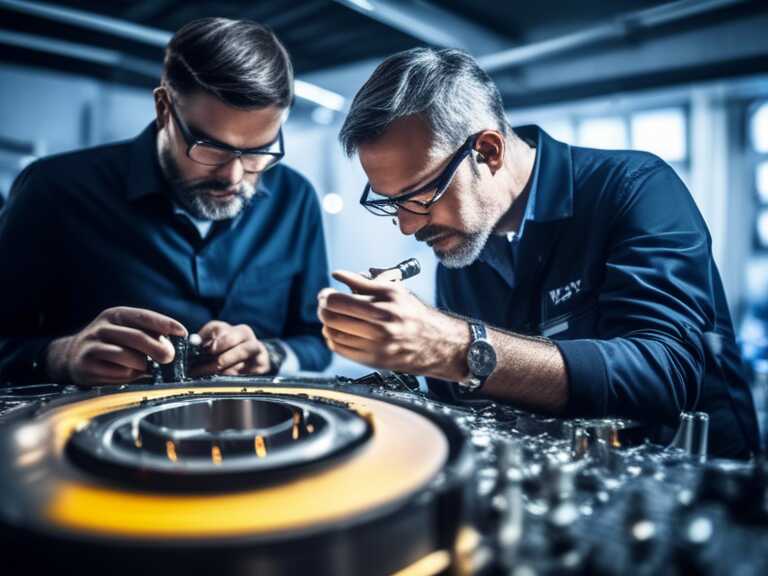
El avance constante en la industria aeroespacial busca optimizar la eficiencia y la resistencia de las estructuras aeronáuticas. En este contexto, la colaboración entre el Instituto Nacional de Investigación Aeronáutica (NIAR) de la Universidad Estatal de Wichita, Estados Unidos y el fabricante alemán KraussMaffei ha dado lugar a innovaciones significativas en la construcción ligera termoplástica.
Un ejemplo tangible de esta colaboración es la utilización del proceso FiberForm de KraussMaffei para fabricar un componente estructural complejo, con una intrincada estructura de nervaduras, diseñado específicamente para aeronaves eVTOL, como los taxis aéreos. Este proceso revolucionario ha reducido drásticamente el tiempo de fabricación en comparación con las técnicas tradicionales metálicas.
El proceso FiberForm consiste en colocar una lámina orgánica (fibras continuas impregnadas con termoplástico) en un molde, conformarla y sobremoldearla. Esta combinación totalmente automatizada de termoformado y sobremoldeo termoplástico ofrece numerosas ventajas respecto a la fabricación convencional de piezas metálicas:
- Disminución significativa de los costes de producción
- Reducción del peso total de las estructuras aeronáuticas
- Un tiempo de producción mucho menor, lo que aumenta la eficiencia
Estas ventajas se logran manteniendo la misma resistencia mecánica y seguridad que ofrecen las piezas metálicas. Además, el proceso FiberForm permite una mayor libertad de diseño, abriendo nuevas posibilidades para la creación de estructuras más ligeras y eficientes.
En el Laboratorio de Tecnologías Avanzadas para Sistemas Aeroespaciales (ATLAS) de NIAR, se lleva a cabo este proceso en una máquina GXW 450-2000/1400 de KraussMaffei con una fuerza de cierre de 4,500 kilonewton (kN), una mesa giratoria y una solución de automatización integrada con dos robots industriales IR.
Las ventajas del tiempo de fabricación reducido son especialmente evidentes en la nueva estructura de nervadura. Tradicionalmente, este tipo de componentes se fresaban a partir de un bloque metálico sólido, proceso que eliminaba más del 80% del material y requería más de 100 horas de procesamiento. En cambio, el componente termoplástico se formó y sobremoldeó a partir de una lámina plana de organolámina en menos de dos minutos.
Además de KraussMaffei, también participaron en este desarrollo las empresas Joby Aviation, Toyota, Victrex y Prospect. El proyecto forma parte del Programa de Fabricación de Compuestos Sostenibles y Asequibles del Laboratorio de Investigación de la Fuerza Aérea de Estados Unidos.
Los resultados ponen de manifiesto el potencial de la tecnología FiberForm para la producción en masa de estructuras primarias y secundarias en la industria aeroespacial. Esta tecnología, originaria de la industria automotriz, abre nuevas posibilidades para la fabricación de componentes ligeros y resistentes, cruciales para la evolución del sector aeroespacial.